The processing of forged and/or cast metal parts often requires a combination of high temperature and a specialized atmosphere. This combination serves to modify the grain structure of the steel part as is necessary for the product’s intended purpose.
Metals Processing
Northeast USA
1600°F (870°C) – Reducing Atmosphere
Metals Processing
Pit Furnace – Electric Element Fired
MaxBlock 2300 Electric Element Modules
Weld-Tite ‘Shoot-On’ Studs
Pit Walls – Unidirectional Construction with Single Strip Battens
Pit Cover – Parquet Construction
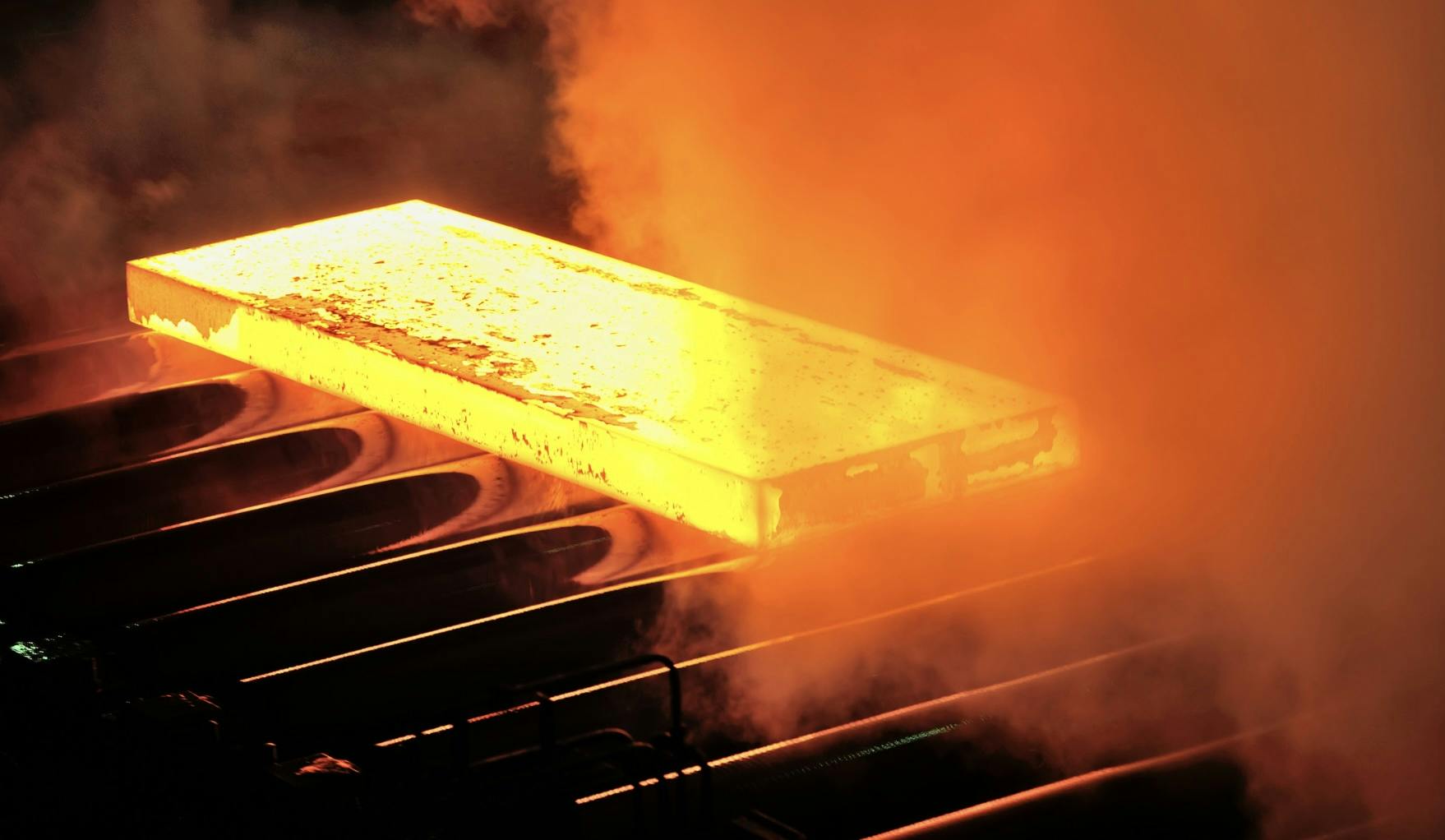
The Challenge
Because of the special atmospheres, traditional fossil fuel combustion systems can’t be used; either the atmosphere lacks oxygen to support combustion or the atmosphere may contain hydrogen which could be potentially explosive.
Critical requirements that owner/operators of atmosphere furnaces have for a fiber lining are:
• The ability to support and be compatible with the non-traditional method of firing the furnace.
• Atmosphere furnaces typically fire intermittently; therefore the refractory system must allow for rapid heat-up and cool-down, and also be immune to thermal shock.
• Low heat storage of the refractory system is necessary in order to allow the maximum amount of available heat energy to be put into firing the product.
The Solution
Due to the atmosphere, an alternative method to fire the furnace is necessary and the use of a rod overbend electric element system is common within the industry. A rod overbend system consists of high temperature alloys which yield resistance when electrical energy is passed through them. As a result, the elements become red hot to heat the furnace. The physical support of a rod overbend electric element system requires a unique module design which must be robust enough to support the electric elements and be electrically insulating to avoid short circuits.
NUTEC partners with an industry-leading electric element manufacturer to provide the complete element and fiber package. The electric element system is custom engineered to meet the customer’s thermal design requirements. NUTEC provides the necessary engineering for the fiber modules and includes all the accessory items which are part of the system. MaxBlock Electric Element Modules have imbedded ceramic tubes that are used to support the metallic electric elements. As the modules are installed, an alignment pin is placed between each adjacent ceramic tube. This alignment pin serves to keep the ceramic tubes straight in line and provides additional strength.
To hang the electric elements in place, ceramic hooks are used; one for each loop of the element row. Ceramic washers are also used to keep the electric elements from contacting the fiber surface of the module. Accommodations are made in the design for lining penetrations and to locate the terminal assemblies that will supply the required voltage to the elements.
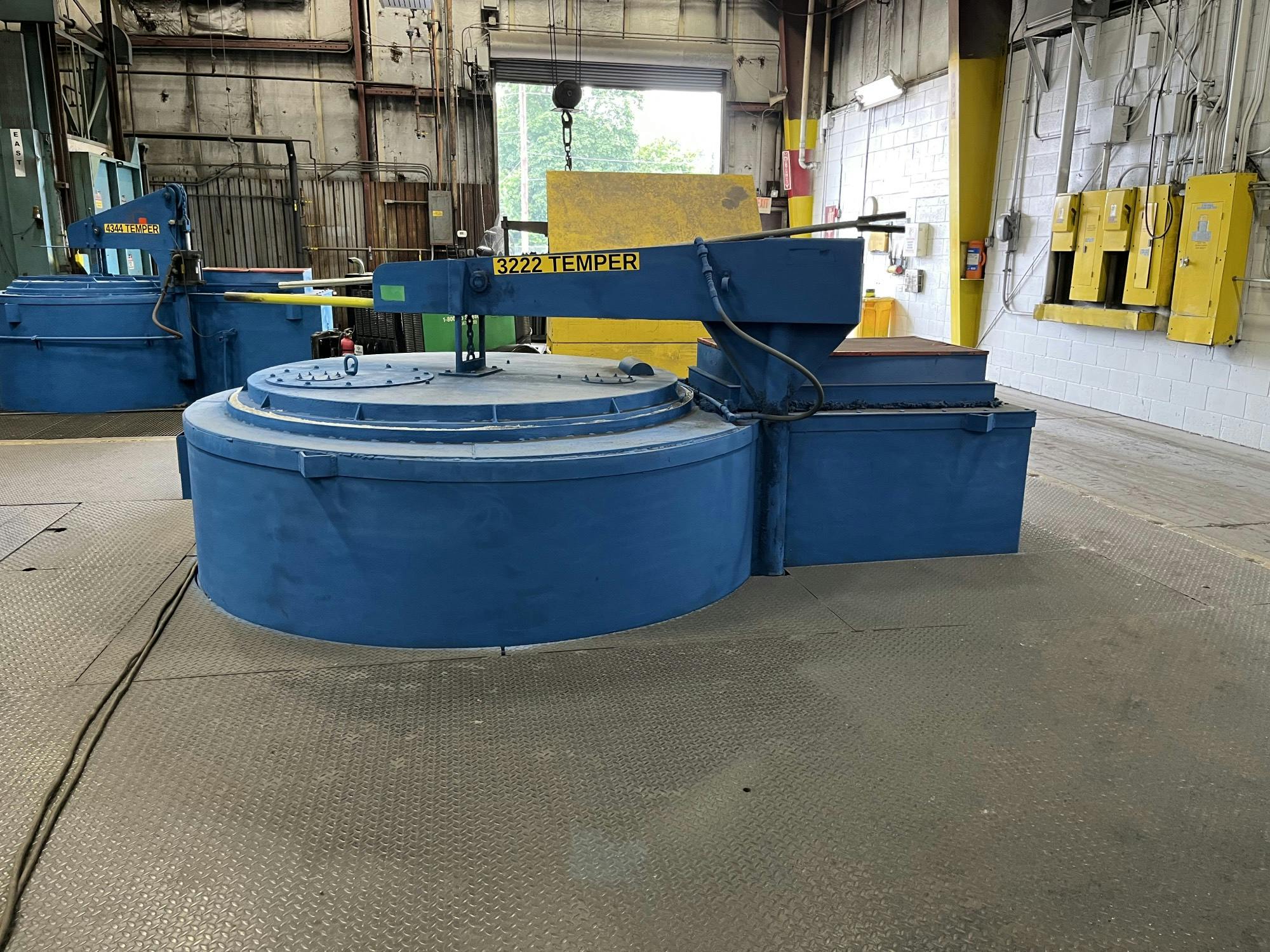
Fig. 1 Typical Pit Furnace
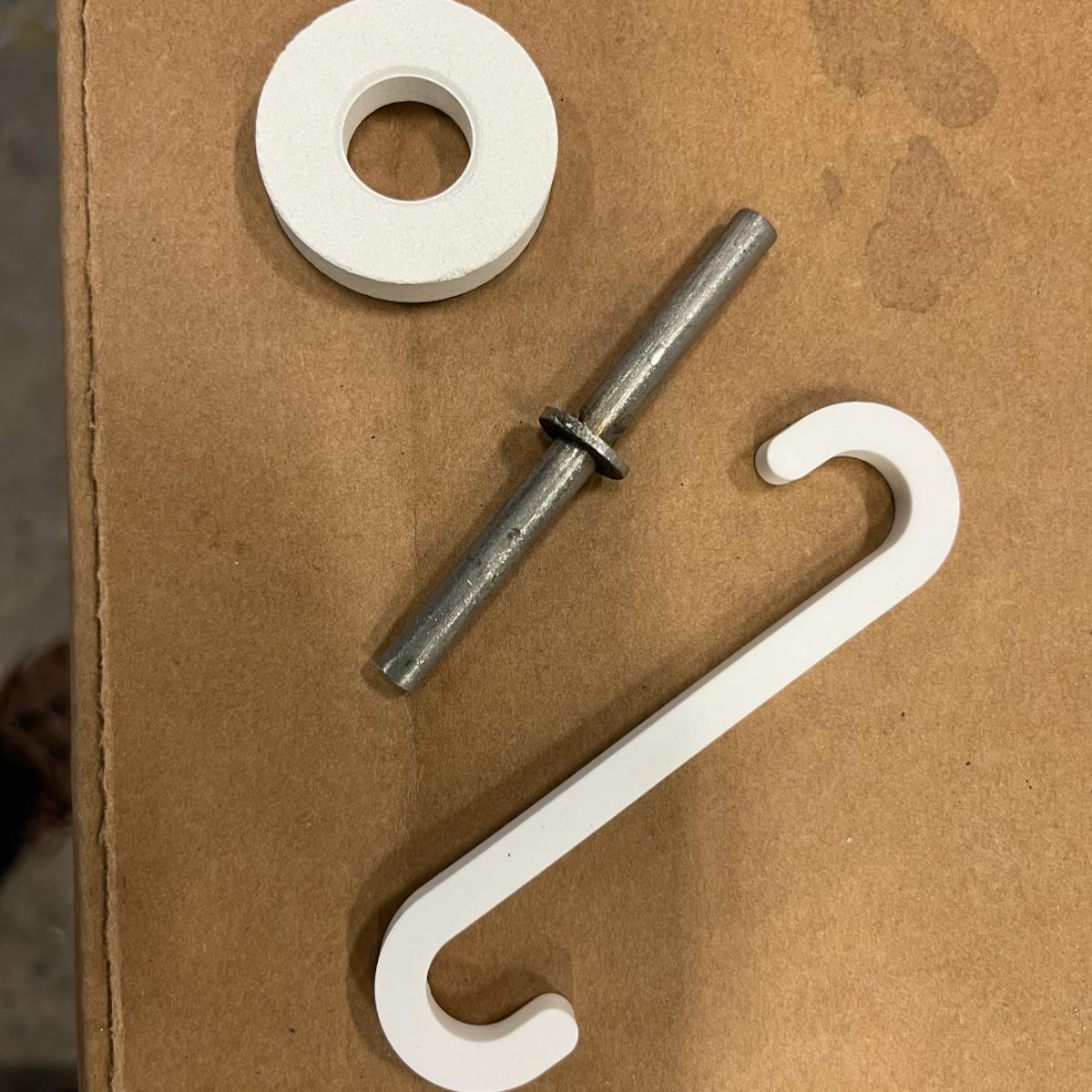
Fig. 2 Alignment Pin, Hook and Washer
Results and Benefits
The MaxBlock Electric Element Module System was installed precisely per the engineered drawings provided by NUTEC for the module system, and by the element vendor for the element system. During the installation, great care was taken to install the modules on their required spacing and with straight rows. The result was a low-density refractory system that can handle the thermal cycling of the application, and can fully support the electrical element heat source.
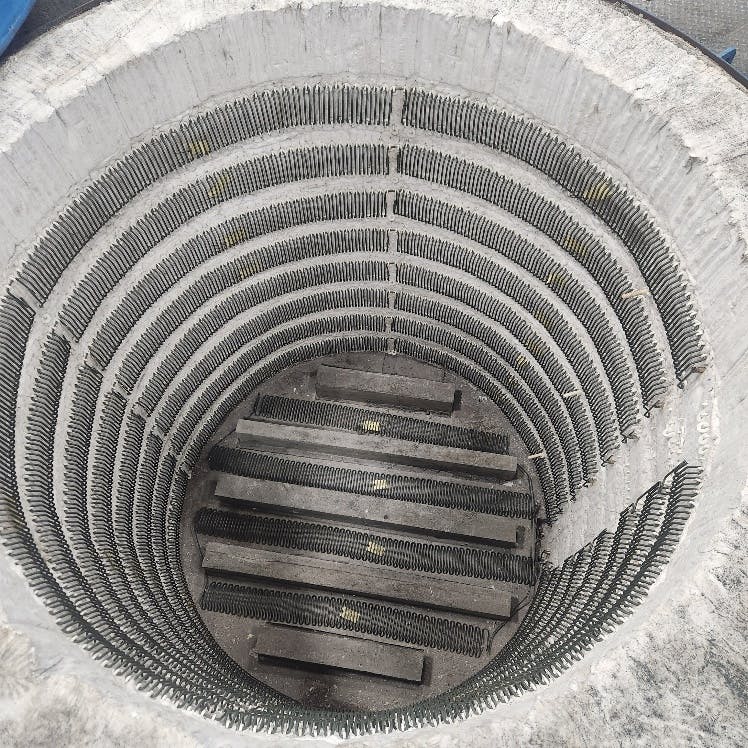
Fig.3 MaxBlock Element Module Pit Furnace
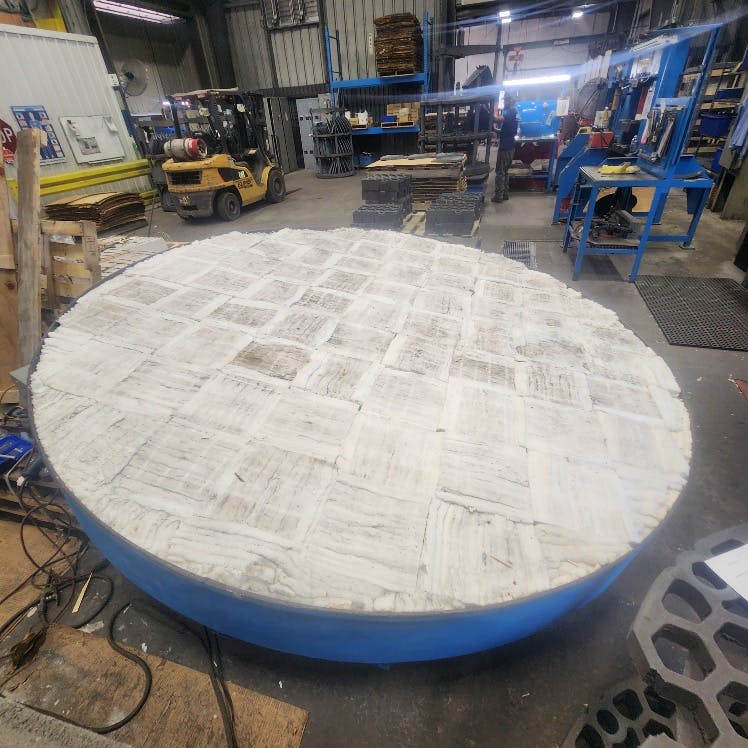
Fig.4 MaxBlock Module Pit Furnace Cover
The Takeaway
Atmosphere furnaces of all types can be very challenging in terms of providing both the necessary heat input for the application and refractory system to match. Standard off-the-shelf products are not normal for these types of furnaces, and a coordinated engineered design between the element system and module providers is very important.
NUTEC has the engineering experience necessary to successfully complete these challenging applications for atmosphere furnaces across all industries.