RTOs are necessary to meet environmental compliance regulations across a variety of industries. Although not part of the actual production process, in most cases industrial facilities are unable to operate unless the RTO is in service. Therefore, a fiber-based refractory system used to insulate the RTO must be durable, reliable, and quickly installed to minimize potential production downtime.
Pollution Control
A Regenerative Thermal Oxidizer (RTO) is a combustion device that controls volatile organic compounds (VOCs), hazardous air pollutants (HAPs), and odors by converting (destroying) the emissions into CO₂ and H₂O through the use of heat, before exhausting them to the atmosphere.
Gulf Coast Region, United States
2000°F (1095°C)
Pollution Control
Regenerative Thermal Oxidizer (RTO)
MaxBlock® 2300 Modules, MaxWool® 2300 Blankets
Prewelded Stud-Tite Studs
Unidirectional Construction with Single Batten Strips
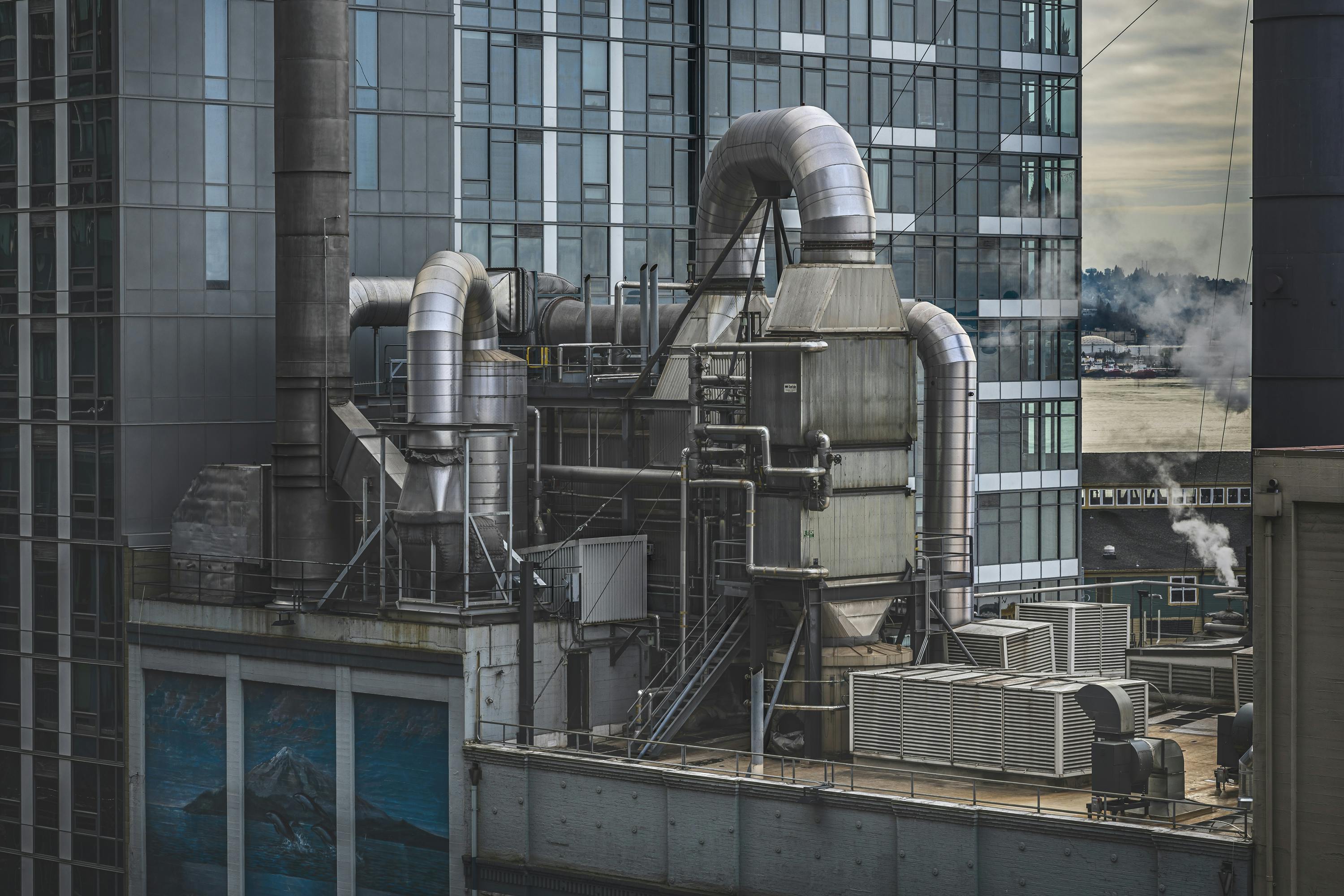
The Challenge
RTO systems commonly contain a bed of catalyst materials that are used to chemically convert VOCs for combustion and release into the atmosphere as CO₂ and water vapor. Over time, these catalyst materials lose their effectiveness and must be replaced. During this replacement, the fiber insulation system is often damaged or requires replacement due to years of service at high temperatures. Critical requirements that owner/operators of RTOs have for fiber lining replacement are:
Installation Ease
Since the RTO is key to operation of the entire facility, downtime for necessary repairs must be kept to a minimum. The fiber refractory package needs to be quickly and easily installed.
Thermal Performance
RTO fiber lining systems are required to last many years. The selection of the fiber products and lining designs used need to ensure long-lasting service. A refractory package that is energy efficient and immune to thermal shock is required for this application.
System Weight
Most RTOs are located outside their respective facilities and their mechanical designs consist of basic structural support with an external steel casing plate to which the fiber insulation is attached. It is not practical or economical to have a massive structural steel support which hard refractory systems (bricks and castables) would require.
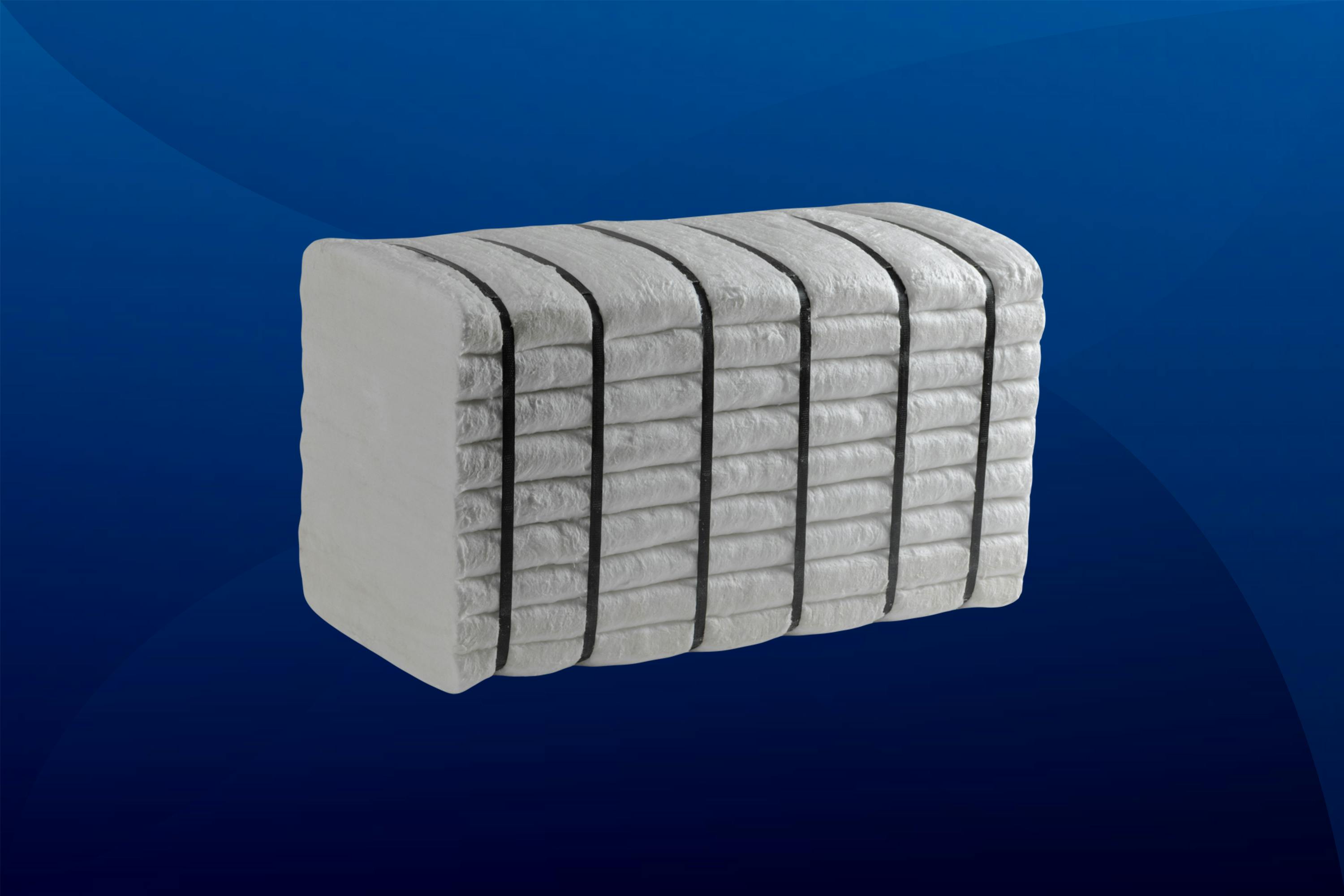
Fig. 1 MaxBlock module
Solutions
In most cases, MaxBlock 2300 (ceramic fiber) or SuperMag 2200 (low biopersistent fiber) are used for RTO applications. The typical lining thickness is 6” (150mm) for the lower regenerative chambers where the catalyst material resides, and 6” to 8” (150mm to 200mm) for the combustion chambers where the conversion of the emissions to CO₂ and water vapor takes place.
For repair and replacement of existing lining materials during a planned shutdown, speed of installation is critical. To meet this requirement, the method of module attachment and the sizes of the modules supplied play an important role.
Results and Benefits
For this particular project, minimizing turnaround time in order to allow the facility to get back into production was critical. To meet this challenge, larger format modules sized at 12” x 24” (305mm x 610mm) were used on the side wall surfaces of the RTO. These larger modules significantly shortened the time needed for installation. NUTEC has the ability to customize its product offering in order to meet customer expectations – such as in this instance, an aggressive installation timeline.
NUTEC's ability to supply larger sized modules with a variety of attachment options also has benefits for new construction. For new construction, fiber installation typically takes place at the OEM’s fabrication facility, and the RTO is shipped out in sections. To minimize both material and labor costs for the OEM, a custom NUTEC offering can be provided.
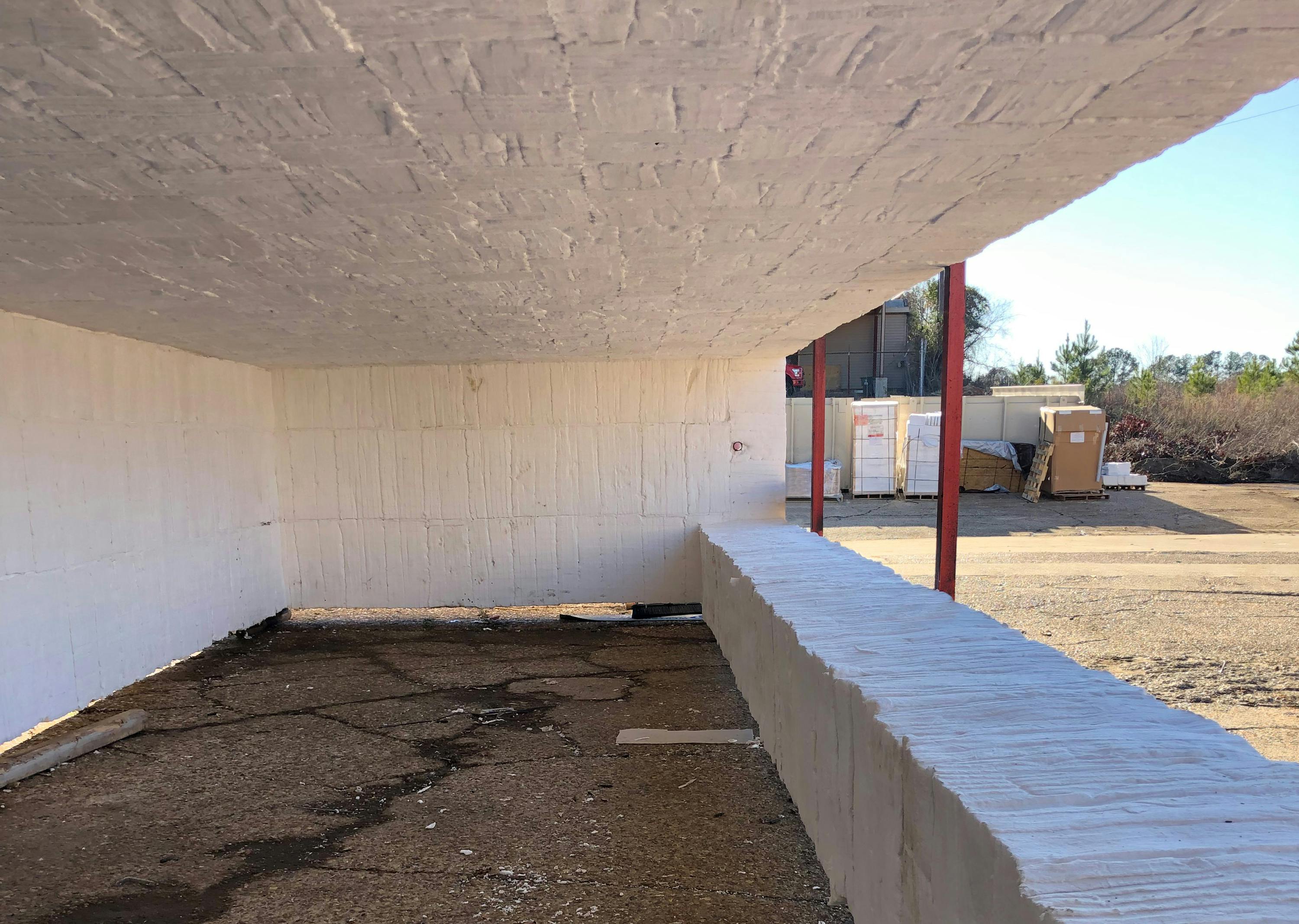
Fig. 2 Typical Combustion Chamber Section
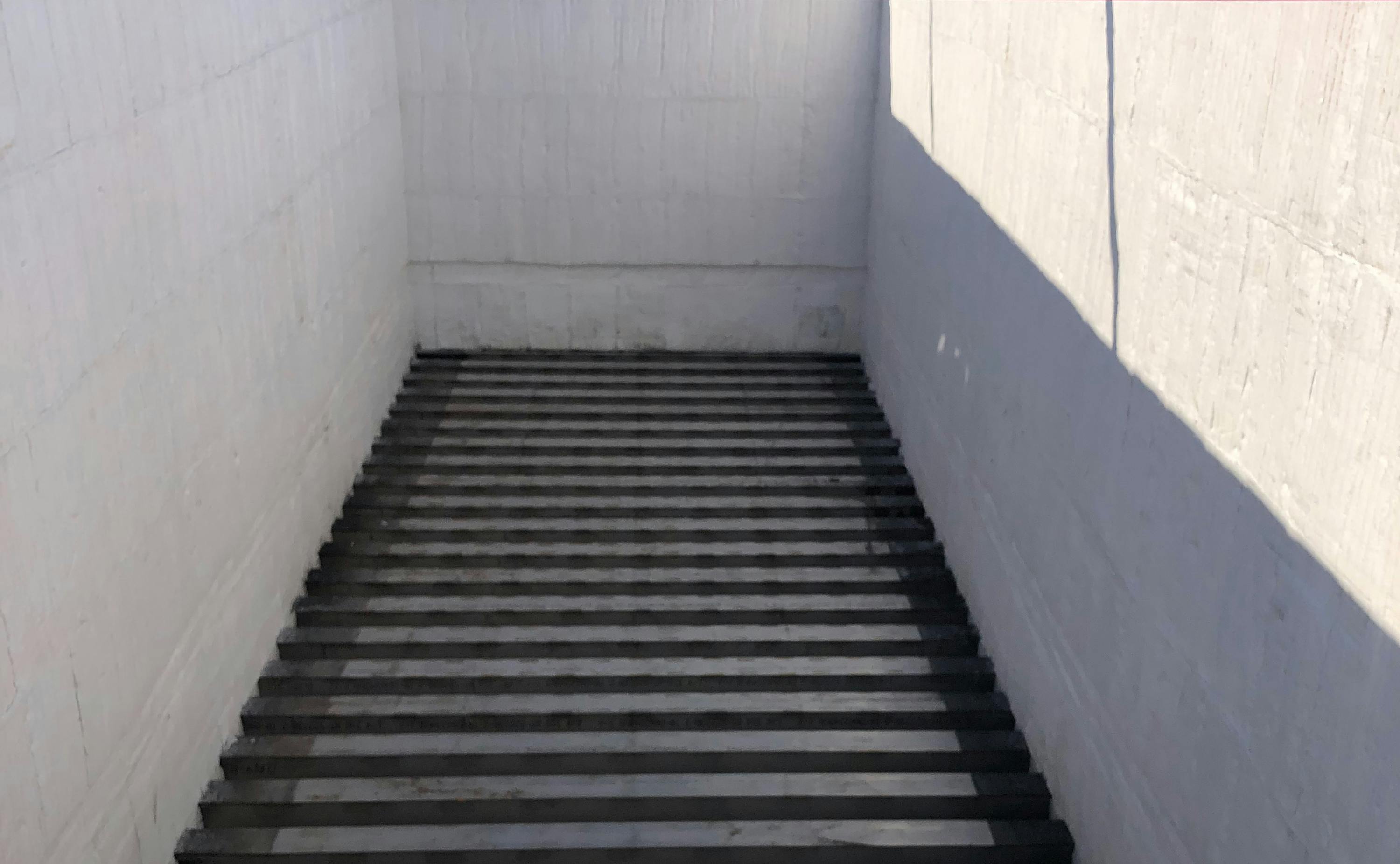
Fig. 3 Typical Regenerative Chamber Section
For this shutdown, NUTEC’s team was able to meet the demanding delivery schedule and provide larger modules that could be quickly installed. As a result, the rebuild of this RTO was completed within the estimated and allocated timeframe, and the facility was able to ramp back up into production as scheduled.
The Takeaway
NUTEC’s experienced Application Engineers and Regional Sales Managers will listen to and fully understand the customer’s requirements. With this feedback in mind, an engineered solution will be provided. If necessary, complete and detailed installation drawings that reflect the recommended design may be provided as part of the quote package.
NUTEC is well positioned to service the RTO market with its broad product portfolio, variety of module attachment options, and ability to customize designs to meet all customer requirements.